Birmingham developer honed in on alternative materials for local projects
By Illyshia Parker, Birmingham Business Journal
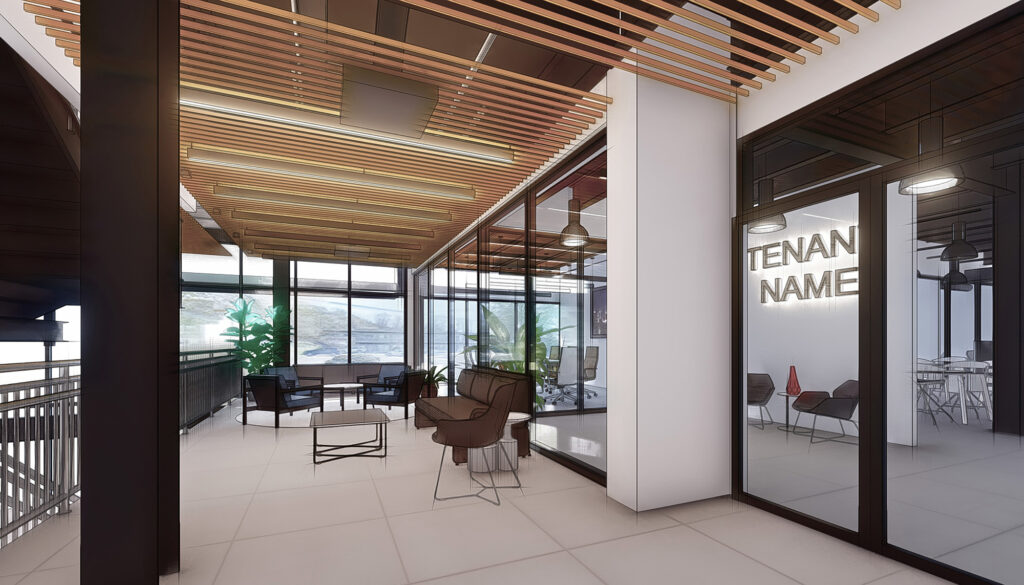
Problems caused by supply chain disruptions are not new, and nothing has curbed the overall demand for new construction across the metro. The demand and need for completed buildings have caused developers to seek out alternatives to get the jobs done in the most effective way.
“The pinch points in the supply chain have morphed throughout the pandemic and have not yet normalized. It’s important to communicate with partners at various levels of the supply chain to find affordable alternates as the disruptions evolve,” said James McCormick, partner and director of construction at D&A Cos.
D&A Cos. is developing The Tramont and 2222 Arlington, both currently under construction in the Redmont neighborhood. According to D&A Cos. partner and co-founder Evan Watts, the company is considering alternatives to imported products for things like wood and tile.
“In lieu of European or other imported cabinetry, we are considering American/North American vendors to source, supply and construct our cabinetry, vanities and other millwork. Similarly, we’ll also be using North American wood flooring in lieu of wood supplied from overseas, as well as local brick/masonry elements and local stones and tile, for example Alabama marble, to compliment a selective use of European stone,” Watts said.
More conveniently located suppliers can reduce material costs and help keep projects on schedule, but the unpredictability of different markets can affect the entire makeup of a structure. According to Van-Tuong Nguyen, project manager, the company experienced this on the 2222 Arlington office project.
“We made modifications because we saw the way the pandemic was going to impact everything,” she said. “We made sure that we had some buffer for the delays in the project. And then it’s just managing the timing. We know that everything’s going to be delayed, and it’s not because of one product; it’s everything across the board.”
D&A Cos. has turned to more domestic products to combat availability and timeliness in some of its ongoing projects.
“Material availability is just as important as cost,” McCormick said. “Sourcing domestic products increases the certainty the material will arrive when you need it. The Tramont will utilize domestically manufactured brick, wood flooring and cabinets to name a few.”
Greener alternatives for both low- and high-rise construction are also being considered for construction projects. D&A Cos. is hoping to use a popular material in European construction.
“One trend that we’re following very closely and have been for a while is CLT construction,” Nguyen said. “Instead of using concrete or steel as your primary structural element, you’re using cross laminated timber, which is a renewable resource. And just because we have a pandemic doesn’t mean that the climate crisis hasn’t gone away. It’s a sustainable material, and we believe strongly in it.”
Read moreDownloadSee project